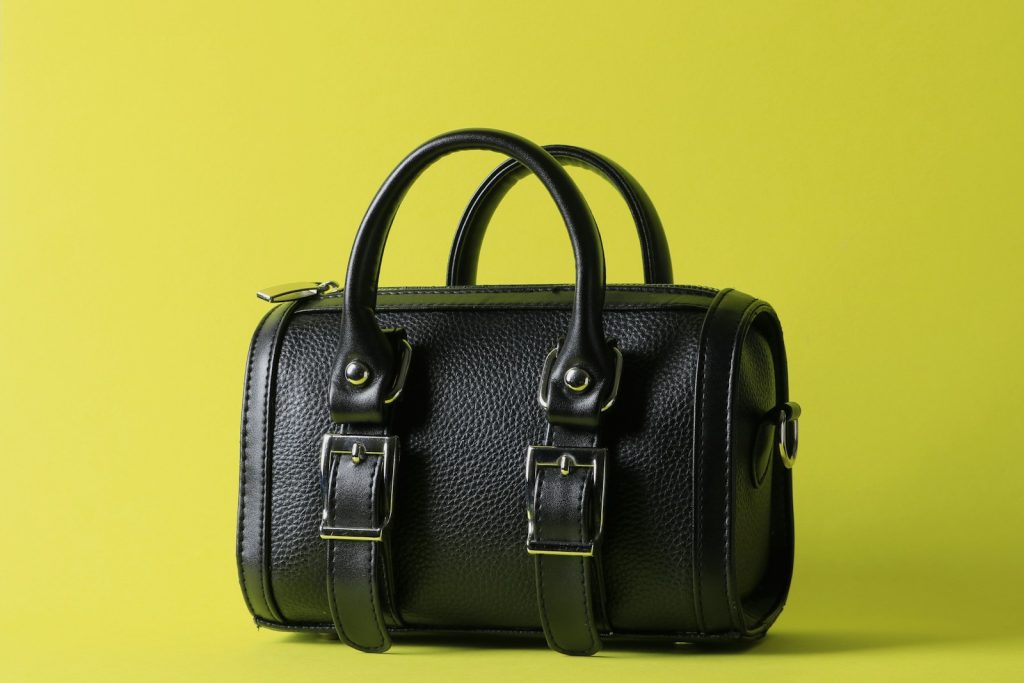
The handbag manufacturing process, while exciting, can come with its fair share of challenges. From quality control to production delays, brands often encounter various issues that can affect the final product. However, with proper planning and effective communication, these problems can be mitigated or avoided entirely. In this article, we’ll explore some of the most common issues in handbag manufacturing and provide practical solutions to ensure a smooth production process.
1. Quality Control Issues
One of the most frequent problems in handbag manufacturing is related to quality control. Even the smallest flaw—whether in stitching, hardware, or materials—can result in an unsellable product or damage your brand’s reputation.
Common Problems:
- Stitching Defects: Uneven or loose stitches can weaken the bag’s structure and give it a sloppy appearance.
- Hardware Failures: Low-quality zippers, buckles, or snaps that break or tarnish quickly.
- Inconsistent Material Quality: Different batches of leather or fabric that don’t match in color or texture, leading to inconsistency in the final product.
How to Avoid It:
- Implement a Strict Quality Control Process: Establish clear quality standards for materials, stitching, and hardware, and ensure these are communicated to your manufacturer.
- Conduct Regular Inspections: Arrange for pre-production sample inspections and mid-production checks to catch issues early.
- Work with Reliable Manufacturers: Choose manufacturers with a proven track record in producing high-quality handbags. Don’t hesitate to ask for references or examples of previous work.
2. Delays in Production Timelines
In the fast-paced fashion industry, delays in production can be a nightmare. Whether it’s due to supply chain disruptions or production bottlenecks, missing a launch date can lead to lost sales and dissatisfied customers.
Common Causes:
- Supply Chain Issues: Delays in sourcing materials or components can push back production schedules.
- Inaccurate Production Estimates: Manufacturers might underestimate how long a production run will take, leading to missed deadlines.
- Unexpected Changes: Design modifications or material shortages that require restarting the production process.
How to Avoid It:
- Set Clear Deadlines: Establish a realistic production schedule that includes buffer time for any unexpected issues.
- Choose Reliable Suppliers: Work with manufacturers who have a stable supply chain and can provide accurate lead times.
- Communicate Regularly: Maintain open lines of communication with your manufacturer to stay updated on production status and address any potential delays immediately.
3. Material Mismatches
Material mismatches can occur when the final product doesn’t use the same quality or type of material that was originally agreed upon. This can affect the look, feel, and durability of the handbag, which can be especially problematic for brands that emphasize premium quality.
Common Problems:
- Wrong Leather or Fabric: Manufacturers might substitute a lower-quality material to cut costs or due to unavailability.
- Color Inconsistencies: Different dye lots can result in handbags with slightly different shades, leading to inconsistencies in your product line.
- Texture and Thickness Issues: Variations in the texture or thickness of leather or fabric can affect the overall look and feel of the product.
How to Avoid It:
- Insist on Sample Approvals: Always approve material samples before production begins. This gives you the opportunity to check the quality, color, and texture.
- Pre-Production Checks: Conduct thorough pre-production checks to ensure that all materials meet your brand’s specifications.
- Work with Trusted Suppliers: Build relationships with reliable suppliers who consistently provide high-quality materials.
4. Design Misinterpretation
A common frustration in handbag manufacturing is when the final product doesn’t match the original design. Misinterpretations of design specifications can lead to incorrect dimensions, poorly executed features, or changes that alter the product’s aesthetic.
Common Problems:
- Incorrect Dimensions: The final handbag may be larger or smaller than intended, affecting its functionality and appeal.
- Design Changes Without Approval: Manufacturers might alter the design to simplify production or reduce costs, leading to an inferior product.
- Misunderstood Details: Complex design elements, such as unique stitching patterns or hardware placements, can be overlooked or poorly executed.
How to Avoid It:
- Provide Clear and Detailed Design Specifications: Ensure your manufacturer has a comprehensive understanding of your design, including dimensions, materials, and construction techniques.
- Use Prototypes: Request prototypes before full production to ensure that your design is correctly interpreted and executed.
- Maintain Close Collaboration: Stay involved throughout the manufacturing process to ensure that your design is faithfully reproduced.
5. Minimum Order Quantities (MOQs) and Cost Issues
For smaller brands or those just starting, high minimum order quantities (MOQs) can be a significant barrier to production. In some cases, the manufacturer may impose unexpected cost increases mid-production, impacting your profitability.
Common Challenges:
- High MOQs: Some manufacturers require large orders, which may not be feasible for new or niche brands.
- Price Fluctuations: Changes in material costs or labor can result in higher production costs than originally anticipated.
- Hidden Costs: Additional fees for packaging, shipping, or handling that weren’t accounted for in the initial budget.
How to Avoid It:
- Negotiate MOQs: Look for manufacturers who are flexible with their minimum order quantities, especially if you’re starting with a small production run.
- Budget for Contingencies: Include a buffer in your production budget to account for potential cost increases or hidden fees.
- Lock in Pricing Early: Try to negotiate fixed pricing for your production run to avoid unexpected changes in costs.
6. Miscommunication with Manufacturers
Effective communication is key to avoiding misunderstandings that can lead to production errors. However, working with international manufacturers can present challenges such as language barriers, time zone differences, and unclear expectations.
Common Issues:
- Language Barriers: Misunderstandings due to language differences can result in incorrect materials, designs, or production methods.
- Vague Instructions: Providing unclear or incomplete instructions can lead to mistakes in production.
- Cultural Differences: Different business practices and expectations between your brand and the manufacturer can cause friction or delays.
How to Avoid It:
- Build Strong Relationships: Take the time to build a strong working relationship with your manufacturer. Regular communication fosters trust and ensures that expectations are aligned.
- Use Bilingual Staff: If language is an issue, hire bilingual staff or a third-party consultant who can facilitate clear communication between you and the manufacturer.
- Clarify Expectations: Provide detailed and concise instructions at every step of the production process, and confirm that your manufacturer understands them fully.
Conclusion: Proactive Problem-Solving is Key
The handbag manufacturing process is full of potential challenges, but most can be avoided with proactive planning, effective communication, and strong relationships with manufacturers. Whether it’s establishing strict quality control measures or ensuring that design specifications are crystal clear, taking a hands-on approach will minimize errors and delays.
By working with reliable manufacturers and maintaining open communication, you can ensure that your handbag production runs smoothly, delivering high-quality products that meet your brand’s standards and delight your customers.