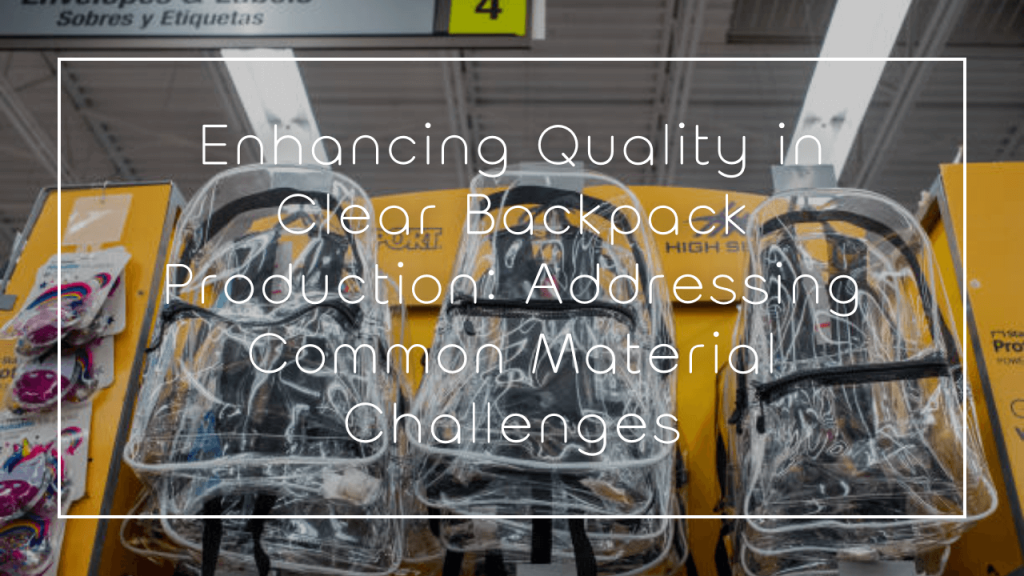
Manufacturing clear backpacks involves certain quality considerations to ensure the final product meets consumer expectations for both usability and longevity. Below are some common material quality issues in the production of clear backpacks, along with potential solutions.
Material Durability
The most common materials used for clear backpacks are PVC (polyvinyl chloride), TPU (thermoplastic polyurethane), and other clear plastic polymers. One main issue is that these materials can tear, puncture, or crack, especially under stress or extreme weather conditions.
Solution: Manufacturers need to ensure the materials used are of high quality, perhaps by selecting thicker or premium-grade plastics that are resistant to tears and punctures. Incorporating reinforcement at stress points, such as the bottom of the backpack and around the zippers, can also increase durability.
Poor Seam Quality
The points where the material is sewn or fused together to create the backpack are critical. Weak seams can result in rips and tears, especially when the backpack is loaded with heavy items.
Solution: Producers can use stronger seams (double stitching, for example) or welding for materials like PVC, which ensures the seams are as strong as the material itself.
Zipper Malfunction
Zippers are often a weak point in backpacks. They can easily break or derail, rendering the backpack unusable.
Solution: Opting for high-quality zippers, possibly with some form of protective casing, can prevent common issues. Additionally, including a warranty or repair policy can increase consumer trust.
Chemical Odor and Health Concerns
Lower-quality clear plastic materials can emit a strong chemical smell, and there may be concerns about the health implications of chemicals used in the plastics, such as phthalates in PVC.
Solution: Using materials that are compliant with health and safety regulations is crucial. TPU, for example, is a safer alternative to PVC and doesn’t have the same odor issues. Communicating the safety and compliance standards followed in production can also reassure consumers.
Scratch and Cloudiness Resistance
Clear materials often become scratched, cloudy, or discolored over time, which can affect the appearance and visibility through the backpack.
Solution: Adding a scratch-resistant coating or layer could help extend the life and clarity of the material. Additionally, manufacturers can provide care instructions to help users avoid actions that contribute to scratching and cloudiness.
Environmental Impact
The environmental footprint of the materials used, especially PVC, is a growing concern among consumers. PVC is not easily recyclable, and its production and disposal contribute to environmental pollution.
Solution: Consider eco-friendlier materials like TPU or recycled plastics, or establish a recycling program for the product. Clearly communicate the environmental efforts of the brand to the market.
Addressing these issues requires a combination of selecting high-quality materials, employing skilled craftsmanship, ensuring compliance with safety standards, and maintaining transparency with consumers regarding product information. By taking these steps, manufacturers can improve the quality of their clear backpacks and gain the trust and loyalty of their customers.