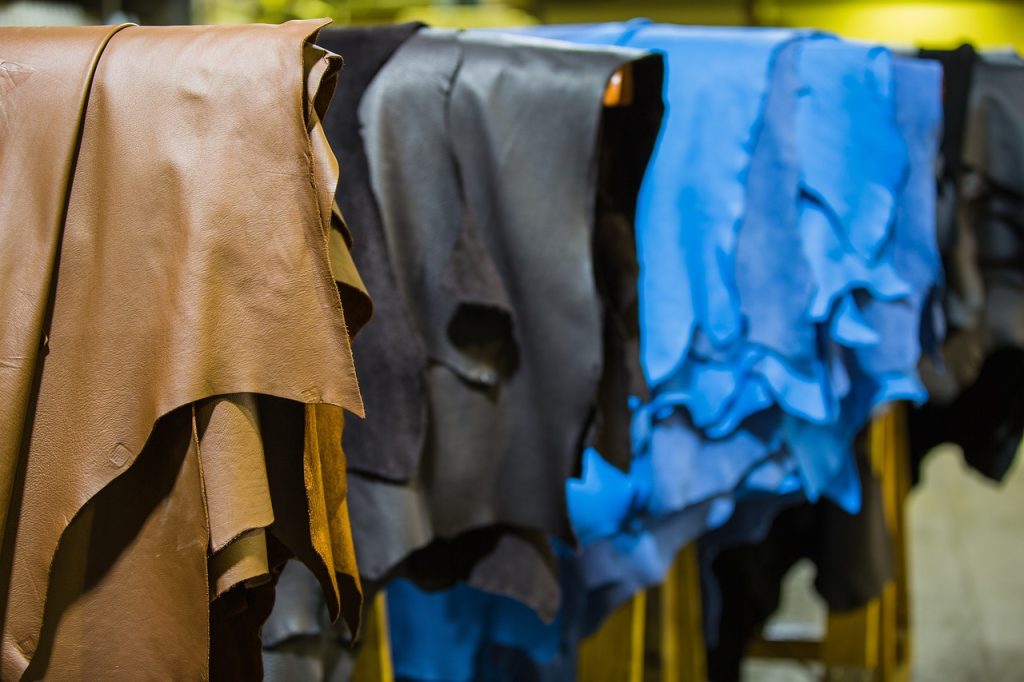
In the highly competitive world of handbag manufacturing, quality and consistency are paramount. Missteps in production not only compromise the product but also impact a brand’s reputation, causing issues in customer loyalty and potential revenue loss. In this article, we address some of the most common errors in handbag manufacturing and provide strategies to avoid them, helping your brand maintain the highest standards of craftsmanship and quality.
1. Subpar Material Quality
Materials form the very foundation of handbag manufacturing. Using low-quality leather or synthetic fabrics can lead to premature wear, discoloration, or poor durability, all of which significantly diminish the product’s longevity and appeal.
How to Avoid Material Quality Issues:
- Source Reputable Suppliers: Partner with suppliers who can guarantee high-grade leather, fabric, and hardware components.
- Perform Rigorous Quality Checks: Conduct strict inspections for each batch to detect early signs of inconsistency.
- Opt for Premium Materials in High-Stress Areas: Focus on durable materials in areas prone to stress, such as straps, zippers, and inner lining.
2. Poor Stitching and Finishing Techniques
Stitching issues, such as loose threads, uneven seams, or visible glue marks, create an impression of substandard quality. In luxury handbags, every stitch and fold reflects the craftsmanship of the brand, making proper finishing an absolute necessity.
How to Avoid Stitching and Finishing Issues:
- Invest in Skilled Labor: Skilled workers understand the nuances of stitching and can maintain consistency throughout production.
- Implement Quality Control Measures: Inspect each piece for symmetry and consistency, ensuring stitches are uniform and no threads are left loose.
- Regularly Service Machinery: Prevent equipment failure and ensure precision by regularly maintaining and calibrating sewing and cutting machines.
3. Inaccurate Pattern Cutting
Precision in pattern cutting is crucial. Errors in this step can affect the symmetry, size, and overall balance of the handbag, resulting in poor aesthetics and functionality.
How to Avoid Pattern Cutting Issues:
- Use Computerized Cutting Machines: These machines provide accuracy that’s hard to achieve manually, reducing human error in pattern cuts.
- Regularly Update Templates and Measurements: Use updated, accurate templates, especially when working with new designs or custom orders.
- Train Staff on Precision Techniques: Provide specific training for staff on maintaining consistency during the pattern cutting phase.
4. Misalignment of Hardware and Fasteners
Hardware like zippers, buckles, and clasps can make or break a handbag’s functionality and aesthetic. Misalignment or poor installation of these components can result in bag closures that don’t function correctly, causing frustration for the user and damaging the brand’s image.
How to Avoid Hardware Misalignment Issues:
- Use Laser Positioning Tools: These ensure accurate placement of hardware elements on each bag.
- Conduct Functional Testing: Check every zipper, clasp, and buckle to ensure smooth operation and secure attachment.
- Standardize Measurements and Angles for Hardware Placement: Keep precise measurement records for consistent hardware positioning across different production batches.
5. Inconsistent Color Matching
Color is a defining feature in handbag design, and even slight discrepancies can ruin the visual appeal of a bag collection. Issues like color fading, mismatched dye lots, or inconsistent shade variations create products that don’t meet design specifications.
How to Avoid Color Matching Issues:
- Use High-Quality Dyes: Low-grade dyes may fade quickly or be affected by environmental exposure. Invest in high-quality, durable dyes.
- Test for Colorfastness: Subject materials to UV light and water tests to ensure color stability and resistance to fading.
- Adopt a Batch Control System: Separate materials by dye lots to ensure consistency in color and avoid visible differences in final products.
6. Flawed Edge Finishing
Unfinished edges on a handbag can lead to fraying, cracking, or peeling over time, reducing the bag’s aesthetic appeal and durability. Proper edge finishing provides a polished look and protects the material from wear and tear.
How to Avoid Edge Finishing Issues:
- Use Quality Edge Paints and Sealants: High-quality edge paints and sealants are less likely to crack or peel.
- Ensure Even Application: Apply multiple, thin coats to edges for a smooth, durable finish.
- Invest in Edge Polishing Equipment: Specialized equipment can create professional, long-lasting finishes that reflect premium craftsmanship.
7. Incorrect Lining Choices
Handbag linings contribute significantly to the bag’s durability, aesthetics, and overall customer experience. A poor lining choice can lead to staining, tearing, or general discomfort for users.
How to Avoid Lining Issues:
- Choose Durable, Stain-Resistant Fabrics: Select linings that can withstand the wear and tear of everyday use.
- Secure Proper Attachment: Avoid loose or bunched linings by attaching them securely to the bag structure.
- Match Lining Color and Texture with Exterior Design: Harmonize the interior lining with the bag’s exterior to create a cohesive and stylish look.
8. Misjudging Size Specifications
Designing bags without accurate size specifications can lead to inconsistent or ill-fitting products. This is particularly crucial in cases of custom or bulk orders where exact dimensions are specified by clients.
How to Avoid Size Specification Issues:
- Create Detailed Size Guides and Prototypes: Before full production, test prototypes to confirm they meet specified dimensions.
- Employ a Pattern Grader: A professional pattern grader ensures precise sizing, preventing discrepancies across batches.
- Consistently Update Measurement Equipment: Calibrate and maintain measuring tools to avoid deviations in product size.
9. Lack of Quality Control in Packaging
Packaging might seem like a minor step, but it plays a critical role in protecting the product during transport and shaping the customer’s first impression. Poor packaging can lead to scratched hardware, crushed shapes, or overall damage to the handbag.
How to Avoid Packaging Issues:
- Choose Appropriate Packaging Materials: Use padded materials, boxes, and dust bags to protect products effectively.
- Conduct Drop Tests: Ensure packaging is sturdy enough to withstand handling and transportation.
- Label with Care Instructions: Include instructions for unpacking and product care, providing a premium experience for customers.
10. Skipping the Final Inspection
A final inspection phase ensures that the product delivered is free from manufacturing flaws and meets quality standards. Skipping this step can lead to avoidable errors reaching the customer, potentially harming the brand’s image.
How to Avoid Final Inspection Issues:
- Institute a Final Inspection Protocol: Create a checklist of all quality parameters to be reviewed before packing and shipping.
- Employ Experienced Quality Control Staff: Skilled inspectors can quickly identify flaws that may go unnoticed during production.
- Automate Quality Checks When Possible: Use software or devices to standardize quality inspections, increasing precision and reducing human error.
Conclusion
The journey from design to the final product in handbag manufacturing is filled with challenges, yet each step can be optimized for quality with meticulous planning and attention to detail. Avoiding these common pitfalls ensures a more consistent, high-quality product, leading to greater customer satisfaction, enhanced brand loyalty, and reduced return rates.