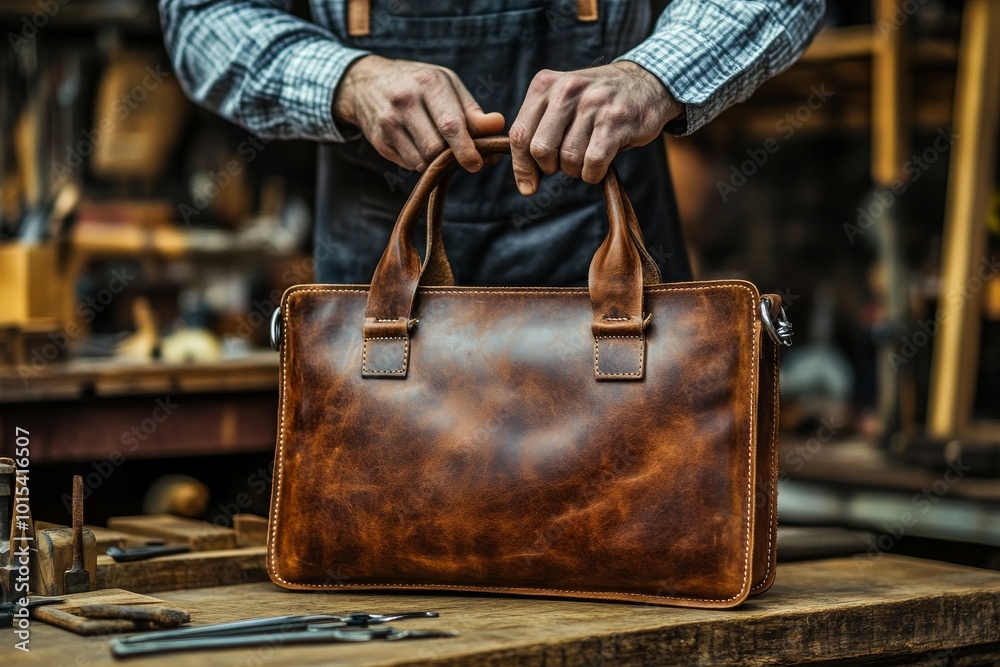
In the ever-evolving world of handbag manufacturing, small-batch production has become a game-changer, allowing brands to test designs, keep inventory costs low, and quickly respond to market trends. However, optimizing the process is essential to ensure efficiency, reduce waste, and maximize profitability. Here, we provide a comprehensive guide on optimizing small-batch handbag production so brands can stay competitive and agile.
What is Small-Batch Production in Handbag Manufacturing?
Small-batch production involves producing a limited quantity of handbags within a controlled timeframe, often for brands seeking to balance quality and uniqueness. Unlike mass production, small-batch manufacturing focuses on exclusivity and adaptability, making it ideal for niche brands, startups, or companies aiming to minimize environmental impact.
Benefits of Small-Batch Production for Handbag Brands
Small-batch handbag production has numerous advantages, including flexibility, cost management, reduced wastage, and quicker go-to-market times. By managing a smaller quantity, manufacturers can ensure higher quality control and cater to customizations, which helps brands appeal to discerning, trend-driven consumers. With the rise of sustainable practices, small-batch production allows companies to produce only what they need, avoiding excessive surplus and environmental impact.
Key Steps to Optimize Small-Batch Handbag Production
Optimizing the small-batch production process for handbags requires a strategic approach, from initial design to final distribution. Here’s how to achieve efficiency and excellence in every stage of the process.
1. Streamline Design and Prototyping
Creating a streamlined design and prototyping phase is essential. A well-organized design stage allows brands to identify potential production issues early on.
- Focus on Standardized Components: By using standardized hardware, threads, and materials across different designs, you can significantly reduce time and costs associated with sourcing unique components for each batch.
- Leverage Digital Prototyping: Using software to create digital prototypes reduces the need for physical samples, which can save time and costs during this phase. Brands can spot design issues and make adjustments before going into production.
2. Source Materials Efficiently
Sourcing high-quality materials efficiently is crucial for small-batch production. Brands often face challenges with material minimum order quantities (MOQs), making it essential to work with suppliers who cater to small-scale needs.
- Build Relationships with Flexible Suppliers: Look for suppliers who specialize in small-batch or custom orders. Some suppliers even offer eco-friendly options, which appeal to sustainably minded consumers.
- Negotiate Lower MOQs: Establishing relationships with suppliers who are open to lower MOQs or who can reserve specific materials for your brand can streamline the supply chain and ensure material availability.
3. Implement Lean Production Techniques
Lean production methods minimize waste, optimize workflows, and enhance efficiency in small-batch production environments.
- Employ the Just-in-Time (JIT) Method: JIT minimizes stock storage needs and reduces overhead costs by producing items only when they are required. This method works well in small-batch production since the goal is to minimize waste and make the most of limited resources.
- Use Single-Piece Flow: Unlike traditional mass production, where multiple pieces move through each stage, single-piece flow focuses on completing one unit at a time. This reduces the risk of errors and improves quality control.
4. Invest in Skilled Labor and Training
Skilled craftsmanship is a hallmark of high-quality handbags, and investing in skilled labor is critical to optimizing small-batch production.
- Hire Skilled Artisans: For premium handbag brands, the quality of craftsmanship is a top priority. Hiring skilled artisans ensures attention to detail, especially for leather cutting, stitching, and finishing processes.
- Continuous Training: Providing training for workers ensures they remain adept at the latest techniques and technologies, such as using automated cutting tools and stitching machines, which can speed up production while maintaining quality.
5. Utilize Technology to Enhance Production
Technology can transform the production process, especially in small-batch manufacturing, where flexibility and efficiency are essential.
- Automated Cutting and Stitching: Automated machinery for tasks like cutting leather and stitching can reduce manual labor and boost productivity, allowing brands to produce more efficiently.
- Inventory Management Software: Inventory management systems help track material usage, order history, and stock levels in real-time. This data allows manufacturers to place orders just in time, reduce waste, and better meet customer demand.
6. Adopt Quality Control at Every Stage
In small-batch production, quality control should be implemented at every phase to avoid costly recalls or rework.
- Quality Checkpoints During Production: Set up checkpoints at key stages of production, such as material inspection, pre-assembly, and final assembly, to catch errors before they become significant issues.
- Customer Feedback Integration: Using feedback from customers to refine products and processes can help identify and correct flaws in the design and manufacturing process, resulting in better product outcomes and customer satisfaction.
Best Practices for Managing Costs in Small-Batch Handbag Production
Controlling costs is vital in small-batch production, where each unit has a higher cost compared to mass production. Below are some cost-saving practices that won’t compromise quality.
1. Optimize Inventory Levels
Overstocking materials and components can lead to unnecessary costs. By managing inventory efficiently, brands can reduce overhead.
- Implement Demand Forecasting: Using historical sales data and market analysis helps in predicting demand accurately and maintaining optimal stock levels.
- Just-in-Time Ordering: Ordering materials only when they’re needed reduces the need for large storage spaces and minimizes costs associated with excess stock.
2. Reduce Material Waste
In small-batch production, each piece of material counts. Implementing waste reduction practices can save on costs without sacrificing quality.
- Use Efficient Cutting Techniques: Automated cutting tools and strategic leather placement reduce waste by ensuring each cut maximizes the material’s surface area.
- Repurpose Scrap Materials: Scrap leather and other materials can be used for smaller accessories, such as keychains or cardholders, which can be sold separately or as add-ons.
3. Optimize Packaging for Small-Batch Production
Packaging can become a significant cost, especially when producing small batches. Optimizing packaging materials and techniques can lead to significant savings.
- Use Eco-Friendly Packaging: Sustainable, minimalistic packaging appeals to eco-conscious consumers and can save costs associated with custom packaging materials.
- Source Packaging Locally: Ordering packaging materials from local suppliers minimizes shipping costs and lead times, which is essential in small-batch production.
Common Challenges in Small-Batch Handbag Production
Small-batch production presents unique challenges, from fluctuating costs to managing supplier relationships. Knowing what to expect can help mitigate potential issues.
- Higher Cost per Unit: Small-batch production often incurs a higher cost per unit compared to mass production, making cost management essential.
- Sourcing Challenges: Finding suppliers who offer low MOQs and quick turnaround times can be difficult, particularly for brands looking to use unique materials.
- Balancing Customization and Efficiency: In small-batch production, brands often offer customization, which can slow down production. Streamlining processes while accommodating custom orders can be challenging.
The Future of Small-Batch Handbag Production
With consumer preferences shifting toward personalized, sustainable products, small-batch handbag production is set to grow. Brands that invest in streamlined processes, quality control, and efficient technology will be well-positioned to capitalize on this trend.
The fashion industry’s move toward sustainability and ethical production will likely lead more handbag brands to adopt small-batch methods. By prioritizing quality, customer feedback, and efficient production practices, brands can create high-quality, bespoke handbags that resonate with today’s consumers.